TROUBLESHOOTING IN BIOPROCESS ENGINEERING: How can we help you solve your fermentation problem:-
Introduction: Bioprocess engineering plays a crucial role in the production of various valuable products through fermentation, including pharmaceuticals, biofuels, enzymes, and organic acids. However, like any complex process, fermentation is not immune to challenges and issues that can hinder productivity and efficiency. In this blog, we will discuss about the world of troubleshooting in bioprocess engineering during fermentation, exploring common problems, their underlying causes, and potential solutions.
- Contamination: One of the most significant concerns in fermentation is contamination, which can originate from various sources such as air, equipment, raw materials, or even the culture itself. Contaminants can include bacteria, yeast, Molds, and viruses. To troubleshoot this issue, strict aseptic techniques should be implemented, including proper sterilization of equipment, use of sterile raw materials, and maintenance of clean environments. Regular monitoring and testing for contaminants is vital, and if contamination occurs, immediate isolation and identification of the culprit should take place to prevent further spread.
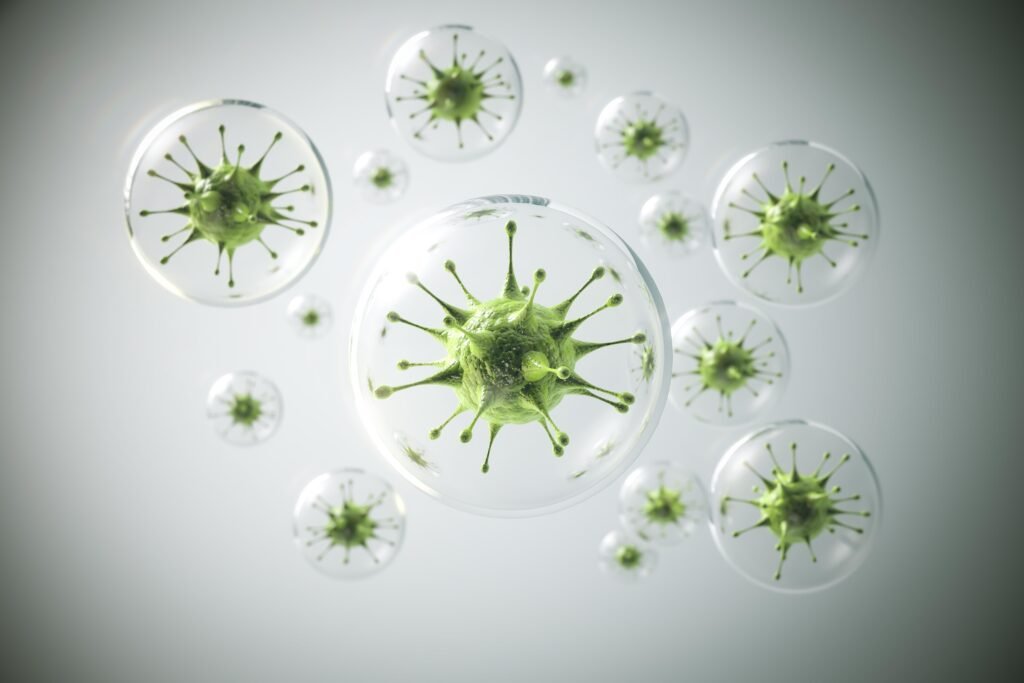
2. Low or Slow Growth Rate: When the microbial growth rate is below the expected level or significantly slower than previous batches, several factors could be at play. Insufficient nutrient availability, improper pH levels, inadequate oxygen transfer, suboptimal temperature control, or high back pressure may contribute to this problem. Conducting a thorough analysis of the fermentation conditions and adjusting the parameters accordingly can help resolve this issue. Ensuring proper mixing and aeration, optimizing nutrient concentrations, monitoring pH and temperature, and addressing back pressure issues are key steps in troubleshooting slow or low growth rates.
3. Foaming and Overflow: Foaming is a common challenge in fermentation, which can lead to equipment overflow, loss of product, and compromised efficiency. Excessive foam is usually caused by the presence of surfactants, proteins, or inadequate control of agitation and aeration. Antifoam agents can be added to reduce foam formation, and modifying agitation and aeration rates can help control foaming. Additionally, adjusting the pH and nutrient concentrations can also troubleshoot/help mitigate foam formation.
4. Product Inhibition: In some cases, the product being produced during fermentation can inhibit the microbial growth and metabolic activity of the culture, leading to reduced yields. This phenomenon, known as product inhibition, can occur due to the accumulation of toxic byproducts or high product concentrations. Strategies to overcome product inhibition include optimizing fermentation conditions to minimize byproduct formation, implementing product removal techniques such as continuous or fed-batch fermentation, or employing genetic engineering to enhance tolerance of the microbial strain.
5. Temperature Fluctuations: Maintaining a stable and optimal temperature is crucial for successful fermentation. Fluctuations in temperature can adversely affect microbial growth, metabolic activity, and product formation. Proper insulation of fermentation vessels, precise temperature control systems, and regular monitoring can troubleshoot temperature fluctuations. Implementing effective cooling or heating mechanisms, such as jacketed vessels or heat exchangers, can ensure temperature stability throughout the process.
6. Back Pressure: Back pressure refers to the resistance encountered by the fermentation system when trying to expel gases, particularly carbon dioxide, produced during the process. High back pressure can inhibit proper gas exchange, impair mixing, and negatively impact the fermentation process. Back pressure can result from various factors, including clogged filters, insufficient venting systems, or excessive foam formation. To troubleshoot back pressure issues, it is crucial to ensure proper venting and gas release mechanisms, maintain clean filters, optimize foam control strategies, and consider the design and capacity of the fermentation system.
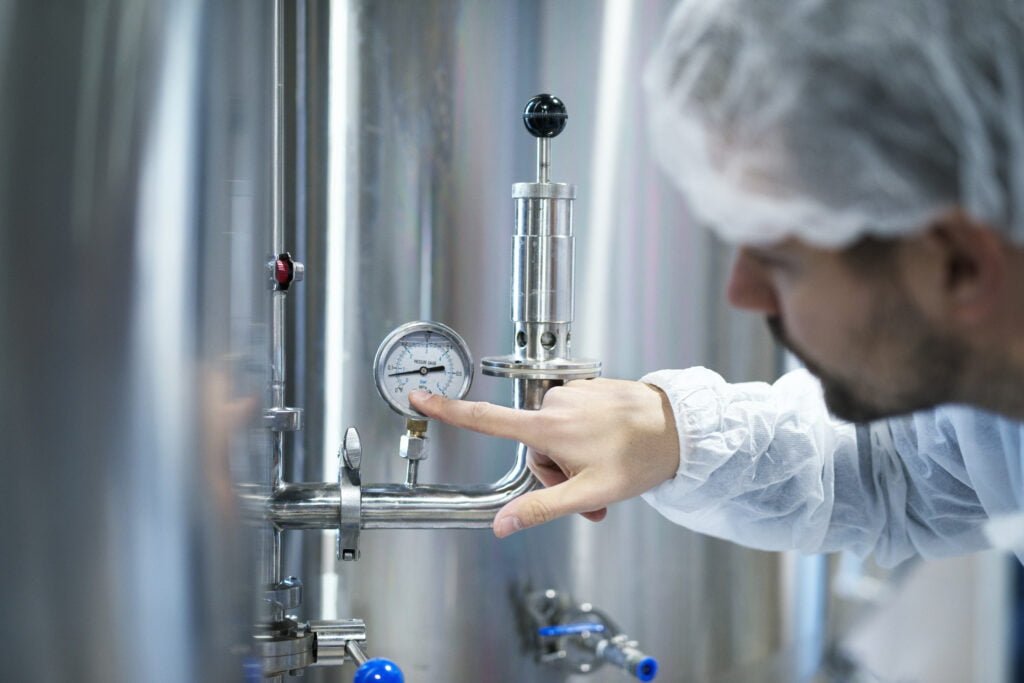
Conclusion: Troubleshooting in bioprocess engineering during fermentation is a multifaceted task that requires careful analysis, attention to detail, and swift action. By identifying and addressing the root causes of common issues such as contamination, low growth rates, foaming, product inhibition, temperature fluctuations, and back pressure, bioprocess engineers can optimize fermentation processes, improve productivity, and enhance the quality of the final products. With consistent monitoring, proactive problem-solving, and continuous process optimization, the challenges in fermentation can be overcome, paving the way for efficient and successful bioproduction.
Frequently Asked Questions (FAQs):
- Q: How can I prevent contamination during fermentation?
A: To prevent contamination, it is crucial to implement strict aseptic techniques. This includes sterilizing equipment, using sterile raw materials, and maintaining clean environments. Regular monitoring and testing for contaminants should be conducted, and if contamination occurs, immediate isolation and identification of the source should take place to prevent further spread.
- Q: What can cause low or slow growth rates during fermentation?
A: Several factors can contribute to low or slow growth rates, including insufficient nutrient availability, improper pH levels, inadequate oxygen transfer, suboptimal temperature control, or high back pressure. Conducting a thorough analysis of the fermentation conditions and adjusting parameters accordingly can help resolve this issue. Ensuring proper mixing and aeration, optimizing nutrient concentrations, monitoring pH and temperature, and addressing back pressure issues are key steps in troubleshooting slow or low growth rates.
- Q: How can I control foaming during fermentation?
A: Foaming can be controlled by identifying and addressing the underlying causes. Excessive foam is usually caused by the presence of surfactants, proteins, or inadequate control of agitation and aeration. Adding antifoam agents, modifying agitation and aeration rates, adjusting pH and nutrient concentrations, and implementing effective foam control strategies can help mitigate foaming issues.
- Q: What is product inhibition, and how can it be overcome?
A: Product inhibition refers to the phenomenon where the product being produced during fermentation inhibits the microbial growth and metabolic activity of the culture, leading to reduced yields. This can occur due to the accumulation of toxic byproducts or high product concentrations. Strategies to overcome product inhibition include optimizing fermentation conditions to minimize byproduct formation, implementing product removal techniques such as continuous or fed-batch fermentation, or employing genetic engineering to enhance tolerance of the microbial strain.
- Q: How can I maintain stable temperatures during fermentation?
A: Maintaining stable and optimal temperatures is crucial for successful fermentation. Fluctuations in temperature can adversely affect microbial growth, metabolic activity, and product formation. Proper insulation of fermentation vessels, precise temperature control systems, regular monitoring, and implementing effective cooling or heating mechanisms, such as jacketed vessels or heat exchangers, can ensure temperature stability throughout the process.
- Q: What can cause back pressure in a fermentation system, and how can it be resolved?
A: Back pressure in a fermentation system can result from factors such as clogged filters, insufficient venting systems, or excessive foam formation. To troubleshoot back pressure issues, it is important to ensure proper venting and gas release mechanisms, maintain clean filters, optimize foam control strategies, and consider the design and capacity of the fermentation system.
Note: – Remember, each fermentation process may have unique challenges, and it is essential to analyse and address specific issues based on the characteristics of the system and the microorganism being utilized. Consulting with experts in bioprocess engineering and fermentation can provide valuable guidance in troubleshooting and optimizing your specific fermentation process.