Concept
of "Material and Energy Balance"
Table of Contents
Toggle
Concept of "Material and Energy Balance"
Table of Contents
ToggleIn the Field of bioprocess Engineering, understanding material and energy balance is crucial. In this article, we will focus on deep understanding of material and energy balance & focusing on how to calculate mass balance in bioprocesses.
WHAT IS MATERIAL BALANCE?
WHAT IS MATERIAL BALANCE?
Material balance (mass balance) is a fundamental concept in bioprocess engineering. It involves accounting for all the materials entering and leaving a system, ensuring that there is no net accumulation within the system. If any change in mass within the system representing accumulation or depletion. This principle established for the foundation for various bioprocesses, ensuring that the quantities of materials involved are carefully tracked and controlled. material balance is essential for tracking the flow of substrates, products, and intermediates within a bioreactor or any other process unit. By maintaining material balance, engineers can optimize resource utilization, minimize waste, and ensure the production of high-quality bioproducts.
Key Elements of Mass Balance:
- Inputs: These are the materials, compounds, or substances that enter the system. Inputs can come from various sources and may include raw materials, chemicals, reactants, or feedstocks.
- Outputs: Outputs are the materials that leave the system. These can be products, by-products, waste, or emissions released into the environment.
- Accumulation: Accumulation refers to the net change in the quantity of material within the system. It can be positive (indicating an increase in material within the system) or negative (indicating a decrease). Accumulation is often a result of reactions, transformations, or storage of materials within the system.
Mass Balance Equation:
The mass balance equation is a fundamental tool used to quantify and ensure the conservation of mass within a system. It is expressed as:
Mass in (Input) = Mass out (Output)+ Mass stored (Accumulation)
In this equation, the total input of materials into the system must be equal to the total output and any accumulation within the system. This principal technique in process engineering, allowing engineers and scientists to design, analyze, and optimize various processes while ensuring that no materials are lost or wasted.
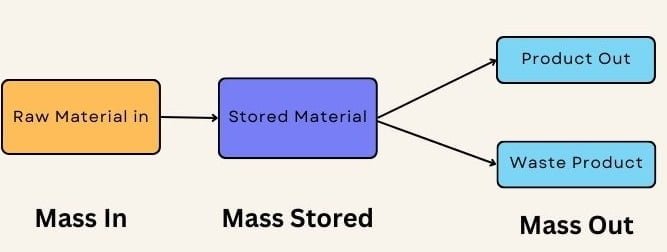
Calculating Mass Balance in Bioprocesses
Now that we have established the significance of material and energy balance, let’s get down to the nitty-gritty of calculating mass balance in bioprocesses. This is where the real magic happens.
Step 1: Define Your System
To begin, you need a clear understanding of the bioprocess system you are working with. Define the boundaries of your system and identify all the inputs and outputs.
Step 2: List Inputs and Outputs
Create a comprehensive list of all the materials and energy sources entering your bioprocess. This could include raw materials, water, chemicals, and energy in various forms.
Step 3: Track Quantities
For each input and output, measure or estimate the quantities involved. Be as precise as possible to ensure accurate calculations.
Step 4: Apply the Mass Balance Equation
The mass balance equation is a fundamental tool for calculating material balance. It is expressed as follows:
Input=Output + Accumulation
In simpler terms, the total input of materials must equal the total output and any accumulation within the system.
Step 5: Account for Accumulation
Accumulation refers to the net change in the quantity of materials within the system. It can be positive (an increase) or negative (a decrease). To maintain balance, you need to account for accumulation accurately.
Step 6: Monitor and Adjust
A successful bioprocess relies on continuous monitoring and adjustment. Regularly check the inputs and outputs, and make adjustments as necessary to maintain equilibrium.
Material Balance in Steady and Unsteady State
Material Balance in Steady and Unsteady State
In addition to steady-state material balance, which we discussed earlier, it’s essential to understand material balance in unsteady-state processes. Let’s briefly differentiate between the two:
Steady-State Material Balance: In a steady-state process, the conditions within the system remain constant over time. This means that the rates of material entering and leaving the system are balanced, resulting in no net accumulation. Steady-state material balance is relatively straightforward, as the parameters do not change with time.
Mass In = Mass Out
Unsteady-State Material Balance: Unsteady-state material balance, on the other hand, deals with processes where conditions change over time. This could be during startup, shutdown, or any transient phase. In such cases, material balance calculations become more complex, as they must consider the changing rates of material flow in and out of the system.
Unsteady-state material balance is essential for understanding how a bioprocess behaves during dynamic conditions, ensuring that it operates safely and efficiently under various scenarios.
WHAT IS ENERGY BALANCE?
Energy balance, on the other hand, focuses on the conservation of energy within a bioprocess system. Just as in mass balance, energy balance is based on the principle of conservation, which states that energy cannot be created or destroyed but can only change forms. Energy balance focuses on accounting for all the energy inputs and outputs within a system. Energy can take various forms, such as heat, mechanical work, or electrical energy. Like material balance, the goal of energy balance is to ensure that there is no net energy accumulation within the system.
In bioprocess engineering, energy balance is crucial for maintaining the optimal operating conditions of bioreactors and other equipment. It helps in controlling temperature, managing heat transfer, and ensuring that the bioprocess operates efficiently.
Key Elements of Energy Balance:
- Energy Inputs: These are the forms of energy that are added to the system, such as heat, electrical energy, mechanical work, or chemical energy from reactions.
- Energy Outputs: Energy outputs represent the energy that leaves the system, which can include useful work done by the system, heat dissipation, or energy losses.
- Energy Accumulation: Similar to mass balance, energy accumulation refers to the net change in energy within the system. It can be positive (indicating an increase in energy within the system) or negative (indicating a decrease). Energy accumulation is essential in understanding how energy is stored or released within a system.
Energy Balance Equation:
The energy balance equation can be expressed in various forms depending on the context and type of energy being considered. However, in its most general form, it can be represented as:
Energy Input=Energy Output+Energy Accumulation
According to this equation total energy input into the system equals the total energy output and any energy accumulation. Energy balance calculations are essential in various applications, such as designing efficient energy systems, optimizing industrial processes, and assessing the environmental impact of energy use.
Principles of Material and Energy Balance
Principles of Material and Energy Balance
The principles governing material and energy balance are based on the fundamental laws of conservation:
Law of Conservation of Mass
This law, often attributed to Antoine Lavoisier, states that mass is neither created nor destroyed during chemical reactions or physical changes. In bioprocess engineering, this law guides the tracking of materials as they move through various stages of a process.
Law of Conservation of Energy
The law of conservation of energy, also known as the first law of thermodynamics, posits that energy cannot be created or destroyed, only converted from one form to another. In bioprocessing, this law underpins the analysis of energy transformations within the system.
Applying Material and Energy Balance
The application of material and energy balance involves a systematic approach:
- Define the System: Begin by clearly defining the boundaries of the system under consideration. What materials and energy are entering and leaving this system?
- Establish Balance Equations: Develop mathematical equations that represent the conservation of mass and energy for the system. These equations serve as the foundation for analysis.
- Data Collection: Gather data on material inputs, outputs, and energy transformations within the system. Precise measurements are crucial for accurate calculations.
- Solve Equations: Use the balance equations to solve for unknown variables or to assess the system’s performance. This step often requires the use of mathematical tools and software.
- Optimization: Identify opportunities to improve material and energy efficiency. Adjust process parameters, equipment, or operational procedures to achieve desired outcomes.
Applications of Material and Energy Balance in
Bioprocess Engineering
Applications of Material and Energy Balance in Bioprocess Engineering
There is various application of material & Energy balance in Bioprocess engineering. Here following application
1. Bioreactor Design and Operation
Bioreactors are central to many bioprocesses, and material and energy balance play a pivotal role in their design and operation. Engineers use these balances to:
- Determine the optimal substrate feed rate to support microbial growth and product formation.
- Monitor the consumption of nutrients and oxygen by microorganisms.
- Regulate temperature and agitation to maintain energy balance within the bioreactor.
- Optimize the removal of metabolic byproducts to prevent their accumulation.
2. Bioprocess Scale-Up
Scaling up bioprocesses from laboratory-scale to industrial-scale is a complex task. Material and energy balance calculations are essential during scale-up to:
- Ensure that the larger bioreactors maintain the same conditions as the laboratory-scale ones.
- Determine the scaling factors for substrate feeding, aeration, and agitation.
- Predict the energy requirements of the larger equipment.
3. Bioprocess Optimization
Efficiency is paramount in bioprocess engineering, and material and energy balance are key tools for optimization. Engineers use these balances to:
- Identify inefficiencies or losses in the process.
- Adjust operating conditions to improve yield and productivity.
- Minimize environmental impact by reducing waste and energy consumption.
Challenges in Material and Energy Balance in
Bioprocess Engineering
Challenges in Material and Energy Balance in Bioprocess Engineering
While material and energy balance are crucial, several challenges exist in their application within bioprocess engineering:
1. Biological Complexity
Biological systems are inherently complex, with variables that can change dynamically. Modeling these systems accurately for material and energy balance calculations can be challenging.
2. Data Availability
Accurate data on microbial kinetics, substrate utilization, and metabolic pathways are essential for precise material and energy balance calculations. Obtaining this data can be time-consuming and resource-intensive.
3. Process Variability
Bioprocesses can be sensitive to variations in raw materials, environmental conditions, and equipment performance. Engineers must account for these variabilities in their balance calculations.
Yield Coefficient:
Yield Coefficient:
In bioprocess engineering, the yield coefficient is a crucial parameter that quantifies the efficiency of a microorganism or biological system in converting a substrate (usually a carbon source) into a desired product, such as biomass, metabolites, or energy. This concept is used to evaluate and optimize bioprocesses for various applications, including biotechnology, wastewater treatment, and biofuel production.
The yield coefficient is typically denoted as Y and can vary depending on the specific substrate and product involved in the bioprocess. There are different types of yield coefficients, including:
- Yield Coefficient for Biomass (Y_X/S): This yield coefficient measures the amount of biomass (microbial cells or other biological material) produced per unit of substrate consumed. It is expressed as grams of biomass (X) produced per gram of substrate (S) consumed. The biomass yield coefficient is crucial in processes like microbial fermentation, where the goal is to maximize microbial growth.
YX/S=Substrate Consumed (S)/Biomass Produced (X)
- Yield Coefficient for Product (Y_P/S): This yield coefficient quantifies the amount of the desired product (metabolite, biofuel, enzyme, etc.) produced per unit of substrate consumed. It is expressed as grams of product (P) produced per gram of substrate (S) consumed. This parameter is vital in bioprocesses aimed at generating specific products.
YP/S=Substrate Consumed (S)/Product Produced (P)
- Yield Coefficient for Energy (Y_E/S): In some cases, especially in the context of microbial respiration or energy generation, the yield coefficient for energy is used. It measures the amount of energy (usually in terms of ATP or another energy unit) produced per unit of substrate consumed. It is expressed as units of energy (E) produced per gram of substrate (S) consumed.
YE/S=Substrate Consumed (S)Energy Produced (E)
The yield coefficient provides critical insights into the efficiency of a bioprocess. A high yield coefficient indicates that the microorganism or biological system is effectively converting the substrate into the desired product, which is often desirable for maximizing production. On the other hand, a low yield coefficient may indicate inefficiency, and process optimization may be necessary to improve yield.
- High Yield Coefficient: A high yield coefficient suggests that the bioprocess is efficiently converting the substrate into the desired product. It indicates good process efficiency and is often desirable for maximizing production.
- Low Yield Coefficient: A low yield coefficient may indicate inefficiency in the bioprocess. It suggests that a significant portion of the substrate is not being converted into the desired product. In such cases, process optimization may be needed to improve yield.
Bioprocess engineers use yield coefficients to design and optimize bioprocesses by adjusting various factors, such as nutrient concentrations, environmental conditions, and microbial strains, to achieve the desired yield. This parameter helps in controlling and predicting the performance of bioprocesses, ensuring that resources are used efficiently, and waste is minimized.
Case Study: Optimizing Fermentation in Bioethanol Production
Case Study: Optimizing Fermentation in Bioethanol Production
Introduction: Bioethanol production is a critical industry that contributes to renewable energy and reduces greenhouse gas emissions. One key step in bioethanol production is the fermentation of sugar-rich feedstocks, such as corn or sugarcane, by microorganisms like yeast. This case study focuses on a bioethanol production facility and how material and energy balance played a crucial role in optimizing their fermentation process.
Challenge: The bioethanol facility was facing challenges in maximizing ethanol yield while maintaining operational efficiency. They needed to address several key issues:
- Yield Improvement: The facility wanted to increase the yield of ethanol from the fermentation process, thereby maximizing the utilization of raw materials.
- Energy Efficiency: Energy costs were a significant concern. The facility aimed to minimize energy consumption while ensuring optimal temperature control during fermentation.
- Waste Reduction: Minimizing waste and byproduct generation was essential to reduce environmental impact and operating costs.
Solution: The facility initiated a comprehensive material and energy balance study to address these challenges. Here’s how it was executed:
Material Balance:
- Raw Material Tracking: The facility meticulously tracked the inflow of raw materials, including sugar-rich feedstock, water, and nutrients, into the fermentation tanks.
- Product Monitoring: Ethanol production and other byproducts were closely monitored to quantify their production rates and ensure no materials were lost or unaccounted for during the fermentation process.
- Waste Minimization: Byproducts, such as carbon dioxide and residual biomass, were evaluated to find ways to minimize waste generation and explore potential uses for these byproducts.
Energy Balance:
- Heat Integration: The energy balance study examined how heat was generated and utilized within the fermentation process. It explored opportunities to recover and reuse heat to reduce energy consumption.
- Temperature Control: Precise temperature control is crucial for fermentation. The facility optimized its temperature control systems to maintain ideal conditions for yeast activity while minimizing energy expenditure.
- Energy Sources: The source of energy for process heating and cooling was assessed, and renewable energy options, such as solar or biomass, were explored to reduce the facility’s carbon footprint.
Results: The material and energy balance study yielded significant improvements for the bioethanol facility:
- Yield Increase: By closely monitoring material flows and optimizing nutrient levels, the facility increased ethanol yield by 10%, leading to higher production rates without increasing raw material input.
- Energy Efficiency: Implementing heat recovery systems and switching to renewable energy sources reduced overall energy consumption by 15%, resulting in cost savings and a reduced environmental impact.
- Waste Reduction: The facility found innovative uses for carbon dioxide byproduct, selling it to nearby greenhouse operations for enhanced plant growth. This not only reduced waste but also generated additional revenue.
Conclusion: This case study highlights how a bioethanol production facility leveraged material and energy balance to optimize their fermentation process. By closely monitoring material flows, improving energy efficiency, and reducing waste, they achieved higher ethanol yields, cost savings, and environmental benefits. This demonstrates the crucial role that material and energy balance play in the sustainable and efficient operation of bioprocess engineering systems.
Case Study: Material and Energy Balance in the Biopharmaceutical
Industry
Case Study: Material and Energy Balance in the Biopharmaceutical Industry
The biopharmaceutical industry is focusing for developing innovative treatments and therapies, often involving complex bioprocesses. In this case study, we will explore how material and energy balance principles are applied in a biopharmaceutical company during the production of a monoclonal antibody, recommending the significance of these balances in ensuring efficient and high-quality production.
Background
Monoclonal antibodies (mAbs) are a class of biopharmaceutical drugs used to treat various diseases, including cancer, autoimmune disorders, and infectious diseases. Their production involves intricate bioprocesses and strict quality control to ensure the safety and efficacy of the final product.
Objectives
The primary objectives of this case study are:
- To illustrate how material balance is crucial for tracking critical components and ensuring product consistency.
- To showcase how energy balance plays a pivotal role in maintaining optimal bioprocess conditions and minimizing production costs.
The Monoclonal Antibody Production Process
Material Balance:
- Cell Culture: The process begins with the cultivation of mammalian cells, which are genetically engineered to produce the desired monoclonal antibody. Material balance is fundamental here, as it ensures that all nutrients, growth factors, and cells are accounted for. This is critical for optimizing cell growth and antibody production.
- Harvesting: Once the cells have reached the desired density and have produced sufficient mAbs, they are harvested. Material balance calculations are used to track the removal of cells from the bioreactor and the recovery of the culture medium.
- Purification: Material balance extends to the purification step, where the mAbs are separated from other cellular components. Precise measurements of the feedstock and output are essential for determining yields and purity.
- Formulation and Fill-Finish: In the formulation and fill-finish stages, material balance ensures that the correct amounts of mAbs, excipients, and buffers are combined to create the final drug product. This step also includes tracking any losses during filling processes to minimize waste.
Energy Balance:
- Bioreactor Operation: Energy balance is critical during bioreactor operation. Temperature control, agitation, and aeration must be optimized to provide the cells with the necessary conditions for growth and mAb production while minimizing energy consumption.
- Purification Process: Energy-intensive steps, such as chromatography and filtration during purification, require careful energy management. Efficient separation techniques and equipment choices can significantly impact energy usage.
- Downstream Processing: Energy balance considerations continue in downstream processing, including formulation, filling, and packaging. Energy-efficient equipment and processes are essential to minimize the environmental footprint and production costs.
Conclusion
In the biopharmaceutical industry, material and energy balance principles are integral to ensuring the efficient and high-quality production of monoclonal antibodies and other biopharmaceuticals. Accurate tracking of materials and energy throughout the production process not only ensures product consistency but also contributes to sustainability and cost-effectiveness. As the industry continues to innovate, mastering these principles remains essential for delivering safe and effective biopharmaceutical products to patients worldwide